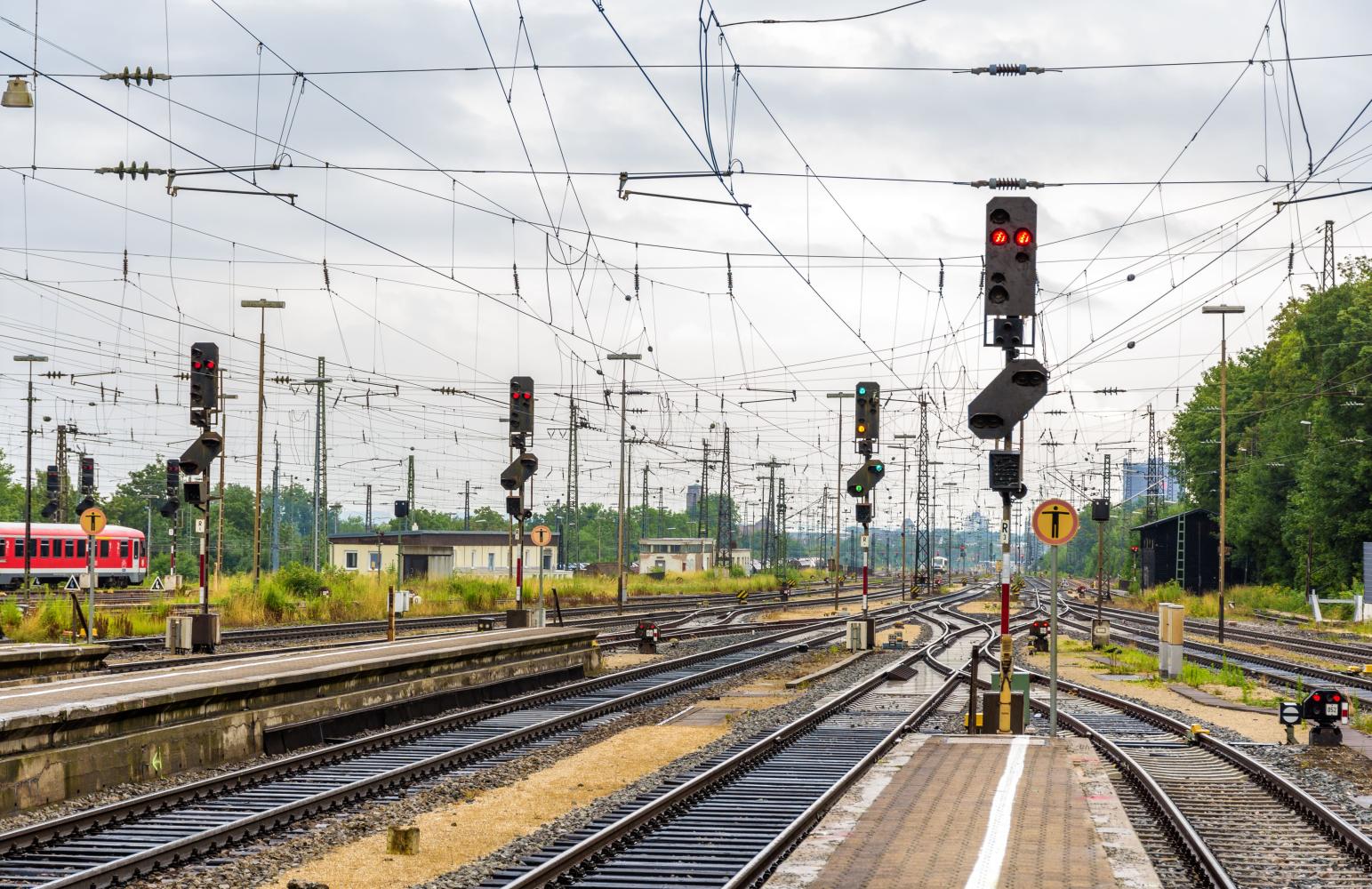
Delivering mission-critical backup power for Europe’s new train protection system
Executive summary
Europe’s railway networks are fast adopting digital interlocking technology as an integral part of their train control systems. This relies on the deployment of many thousands of track field concentrators to communicate with centralized systems and control critical equipment such as signals and barriers. Reliable backup power is vital to ensure continuity of operation. That calls for a new generation of high-tech lithium-ion (Li-ion) battery systems. Saft has moved to meet this demand with a specially adapted version of its Flex’ion™ Gen2 system developed originally for data center UPS applications.
Making the leap from electronic to digital interlocking
Europe’s many previously incompatible train protection systems are evolving into a new integrated approach under the European Train Control System (ETCS). As the signaling and control component of the European Rail Traffic Management System (ERTMS) this brings benefits such as:
- Increased safety and reliability
- Increased train speed
- Increased capacity
- Improved train interaction
The key development for the new generation of ETCS (Level 2 and 3) is that it has evolved from mechanical interlocking, through electronic interlocking to digital interlocking.
Digital interlocking technology
The capability for digital interlocking, together with a standardized integrated control and operating system, is the foundation for digital signaling technology within the ETCS.
Digital signaling technology is a further development of electronic signaling technology that is controlled by a new operating system. This approach replaces the many different types of signal boxes of various designs that have been installed over previous generations. The major difference with digital signaling, compared with electronic signaling, is that control signals are transmitted over a fiber optic link to equipment such as points, barriers and signals. This separation of energy and data offers improved reliability as well as enhanced diagnostic capabilities.
An important advantage of using fiber optics to control trackside equipment is that commands can be issued over a greater distance from the centralized control center. It also enables the use of standardized interfaces as well as condition-based maintenance. Since the standardized interfaces are open and use standardized IP-based internet protocols, components from different manufacturers can be readily interconnected to form an overall system.
Subsystems for digital signaling
The digital signaling system is built up of individual, clearly specified subsystems - sometimes also called components - (central unit, signals, switches, etc.). The key subsystems are the large number of new track field concentrators (known as “GFKs” in Germany), these shed-like enclosures are the connection points for the outdoor field elements. The track field concentrators are in turn served by much larger technology centers (“TSOs” in Germany), but these are generally already in service.
Battery backup power is crucial for safety and reliability
The continuous and uninterrupted operation of the digital signaling systems and the integrated equipment they control is vital for safe and reliable operation. This calls for backup battery power systems to maintain continuity should the main power supply fail. The uninterruptible power supply (UPS) for a data center generally requires battery backup for only a short duration until an emergency generator can be brought online. However, for mission-critical railway signaling applications the situation is different and demands backup for two hours or more.
Li-ion is the backup battery technology of choice
High-tech digital signaling systems demand high-tech backup batteries. Lithium-ion (Li-ion) has emerged as the leading technology for four main reasons:
Intelligence – A unique advantage of Li-ion technology is that it enables advanced battery management through access to key information such as state-of-charge (SoC) and state-of-health (SoH) as well as communication to wider networks via Modbus. This is a key element in both safety and reliability.
Safety - Fire safety is a critical aspect in the selection of backup batteries for UPS installations. Li-ion cathode technologies based on iron phosphates are preferred generally for their improved safety over metal oxides. Phosphates do not contain oxygen that can be relased in the case of a fire (the phosphate bond is too strong) and therefore reach much lower temperatures of around 200 to 250°C, which makes propagation from one cell to another significantly less likely.
The main cathode materials are LFP – Lithium iron phosphate and SLFP – Super lithium iron phosphate. Saft’s phosphate cells have passed all relevant Li-ion standards, in both the EU and US. This includes UL 9540A, on our Power range for example, with no cell-to-cell propagation, no flames and several minutes between venting and thermal runaway – this allows detection systems sufficient time to detect the escape of electrolyte gases and trigger a warning.
A Li-ion battery is a collection of cells that includes protection and communication circuitry. Most Li-ion UPS batteries consist of modules, which are a group of cells with some monitoring circuitry. These modules are then assembled into a rack, together with monitoring circuits, switching circuits and communications electronics. A suitable battery management system (BMS) has multiple layers of protection based on both software and hardware. It is vital to monitor the voltage of every individual cell, as this reacts faster than temperature and is a more reliable safety indicator.
At the system level there are typically additional components such as the local battery management module (BMM), which is responsible for safety within the cabinet itself, and a global master (MBMM). This communicates with the UPS as well as other external applications such as the system information system for visualization of the battery information.
Reliability – Saft Li-ion batteries have a proven industrial reputation for reliability and an expected lifetime of up to 20 years in normal operating conditions.
Flexibility – Saft Li-ion batteries can be configured to suit various voltage, power and energy requirements while matching the narrow DC voltage window required by a UPS.
Flex’ion™ Gen2 System is the ideal battery backup for track field concentrators
Saft’s backup battery solution for track field concentrators is a modified version of the Flex’ion™ Gen2 system developed specifically to deploy the proprietary Li-ion Super-Phosphate (SLFP™) chemistry in UPS and other mission-critical applications. It offers a unique approach since all the key elements are designed and developed in-house - from the individual Li-ion cells, through the battery modules to the cabinet complete with the BMM and human-machine interface (HMI). This integrated, optimized concept delivers high power performance combined with the highest safety levels and a low environmental footprint.
A unique feature of Flex’ion Gen2 is its broad voltage window from 110 to 700 V DC. For the track field concentrators, a 400 V DC busbar is used.
The Flex’ion™ Gen2 concept has passed rigorous testing under the UL 1973 and UL 9540A methods. For example, the PFe version is certified for use:
- without a built-in fire suppression system, placing Flex’ion at the highest level of safety
- without an air separation gap between cabinets, minimizing the space required and the total cost of ownership (TCO) of the data center overall.
Previously, valve regulated lead-acid (VRLA) batteries have been specified for this type of application. However, Flex’ion Gen2 offers several important advantages:
Compact and lightweight - As well as having a smaller footprint, Li-ion batteries are six times lighter than VRLA, making them both easier and safer to handle and reducing the loading on housings and foundations.
Reliable operation at higher temperatures - Flex’ion Li-ion battery technology can operate reliably at high temperatures (35ºC), which can reduce HVAC requirements, minimizing energy and water bills as well as carbon emissions - making a further contribution to a lower TCO.
Long life – Flex’ion Gen2 batteries will have an expected service life of up to 20 years. This is around two to three times longer than VRLA batteries, and as temperatures increase, the life of VRLA batteries decrease dramatically, while the effect is much lower on Li-ion.
Fast recharge – even after a full discharge (following failure of the main AC grid), the Flex’ion Gen2 system can recharge rapidly to ensure maximum availability when the grid is restored.
Low float-charge current - Li-ion batteries consume much less electricity during float charge in comparison with VRLA. So, over a large fleet of track field concentrators, the energy savings could be very substantial. In addition, Flex’ion™ batteries have a charging efficiency of 99%, versus only 75% for VRLA, which further increases the saving in electricity.
Li-ion technology is essential to support the roll-out of digital interlocking technology
In summary, the roll-out of digital interlocking will see the installation of a huge number of track field concentrators across Europe. Ensuring the safe and reliable operation essential for the continuity of rail services demands a high-tech battery solution. Saft’s Flex’ion Gen2 has been developed to meet this demand with features including:
- Fulfillment of all relevant Li-Ion standards, in particular safety
- Proven Industrial reputation
- Lifetime of up to 20 years
- Wide DC voltage window to operate with most types of industrial UPS
- Very low maintenance requirements
- Continuous monitoring
- Built in intelligence and ability to communicate with UPS /control equipment
- Optimized total cost of ownership (TCO)